Share
Pin
Tweet
Send
Share
Send
Maar de ervaring van ambachtslieden laat zien dat je, zelfs zonder het draaiende bedrijf te kennen, een mechanisch hakmes kunt maken van geïmproviseerde materialen, dat het aanpast aan de plaats, het werkvolume en antropometrische gegevens.

Zal nodig hebben
In principe kunnen bijna alle materialen en assemblages voor het assembleren van een mechanisch hakmes uit oude auto's, huishoudelijke apparaten worden verwijderd en op stortplaatsen worden gevonden. Maar het doet geen pijn om te weten hoeveel dit of dat "ding" in de winkel is, hoeveel de motor van de oude wasmachine kost, wat de turner om werk vraagt, enz.
Dus wat moeten we inslaan als we besluiten om een mechanisch hakmes te maken:
- rondgewalst staal (rond hout);
- afplakband;
- plaatwerk van verschillende diktes;
- profielpijp ongeveer 14 m;
- vliegwiel van de GAZ-53;
- bouten, moeren, ringen;
- een motor met een riemschijf en riem;
- verf en penseel;
- conische schroefmes wortel.
Van gereedschap en apparatuur moeten we bij de hand hebben:
- molen met schijven;
- plazmorez;
- bestand voor metaal;
- lasapparatuur;
- bankschroef en klemmen;
- boren met boren.
Productie van knopen en details van een splitter
We bevestigen het ronde hout in een bankschroef en markeren de snijplekken met afplakband voor snelheid en gemak om de gewenste nauwkeurigheid te garanderen.

Volgens de markeringen snijden we de blank van de houtsplijteras met een slijpmachine en een 180 mm-doorslijpschijf.
We markeren het oppervlak van een dikke plaat metaal met twee schijven van verschillende grootte, maar met dezelfde centrale gaten.
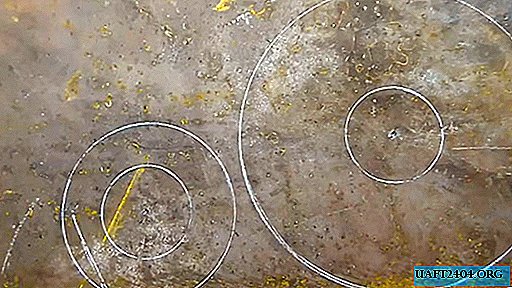
Het is handiger en nauwkeuriger om ze te snijden met een plasmasnijder, waardoor de hoeveelheid latere verwerking wordt geminimaliseerd.
We brengen de schijven op de gewenste grootte met een vijl en een grinder, en om het overtollige metaal niet te verwijderen, plakken we op de zijvlakken de exacte patronen van tape of papier.

De belangrijkste aandacht bij het verwerken van schijven is gericht op de centrale gaten: de schacht van de as moet er vrij in komen, maar tegelijkertijd moeten de openingen minimaal zijn.
Deze bewerking is een van de cruciale: we lassen een grote schijf precies onder de 90 graden op het ronde hout. Daarom voeren we lassen zorgvuldig uit, waarbij we constant de hoek tussen de onderdelen controleren zodat ze niet leiden, en we gebruiken magnetische vierkanten. Wij reinigen lassen.
De tweede ring is eenvoudiger te installeren. Het is voldoende om het stevig aan te drukken en met klemmen op de eerste schijf te bevestigen en in deze positie te lassen.


Nu zal een draaier op het werkstuk werken: het slijpt de voorste steun, die aan de kleinere ring is gelast, cirkelvormige oppervlakken op maat slijpen en een reeks ringgroeven onder de aandrijfriem maken.
Uit de profielpijp snijden we de werkstukken van de vereiste afmetingen en in de vereiste hoeveelheid, waaruit we niet alleen een bureaublad lassen, maar de basis voor het installeren van ook gemonteerde eenheden.


Los daarvan lassen we een subframe aan het hoofdframe onder het aanrecht, waaraan de elektromotor wordt bevestigd en aangepast.

We hebben de molen twee symmetrische delen uit een metalen plaat van 6 mm dik gesneden, die, aan elkaar gelast en op het aanrecht bevestigd, een soort messtop op een houtsplijter zijn.

Omdat de belasting van ons apparaat constant zal veranderen, kunt u niet zonder vliegwiel. In ons geval bleek het GAZ-53 vliegwiel met een buitendiameter van 372 mm, een landingsgat van 40 mm en een massa van bijna 16 kg het meest geschikt in grootte en gewicht.

We verwijderen het tandwiel van dit onderdeel en reinigen het van langdurig olieachtig vuil met behulp van een hamer, een schroevendraaierpunt en een slijpmachine met sproeiers.

We voeren de as en het vliegwiel statisch uit door ze met bouten en moeren aan elkaar te schroeven. Vanwege het ontbreken van een balanceermachine, vinden we het uit met alleen beschikbare contanten.


Plaats hiervoor tijdelijk twee hoeken parallel op het tafelframe en pak ze voorzichtig vast. Met behulp van het niveau bieden we de maximaal mogelijke vlakheid aan de hoeken en plaatsen we een as met een vliegwiel erop.

Geef de rotatie aan het vliegwiel en controleer het stopmoment. Als er een onevenwichtige massa op staat, rolt deze voor het stoppen een beetje terug. Bovendien zal de overtollige massa zich op het laagste punt bevinden. We markeren deze plek en boren een gat, waardoor de overtollige massa wordt verwijderd.

Het balanceren wordt als voltooid beschouwd wanneer de as en het vliegwiel niet terugrollen voordat ze stoppen.
Voor de veiligheid maken we van de overblijfselen van de profielpijp en het plaatwerk een beschermkap op het vliegwiel en koken we het tafelblad.


We verbinden twee symmetrische delen onder een hoek met elkaar, binnen hebben we een afstandsstuk en lassen de resulterende assemblage op het aanrecht.

Alle knooppunten en onderdelen zijn gemaakt, dus ga door met schilderen met een gewone kwast.
Geschatte kosten
Laten we inschatten wat een zelfgemaakte splitter ons zal kosten:
- vliegwiel - 1200 roebel .;
- profielpijp 14 m - 1200 roebel .;
- de motor van de sluitring (730 W, 8000 tpm) - 530 roebel;
- "wortel" (basisdiameter - 70 mm, hoogte - 250 mm) - 1300 roebel .;
- twee 206 lagers in de behuizing - 600 roebel;
- het werk van de keerder - 1650 roebel .;
- hardware en aandrijfriem - 530 roebel.
In totaal blijken er ongeveer 7 duizend roebel te zijn. Dit is 3 keer minder dan de goedkoopste fabriekssplitser.

Assemblage van knopen en details van de splitter
Bevestig het vliegwiel stevig op de as, doe de riem om, draag de eenheden en bevestig de eenheid aan het frame.
We installeren en bevestigen de "wortel" op het aseinde met twee speciale pennen.


We spannen de riem door de daartoe bestemde bout te draaien, die tegen de steun aankomt, de motor duwt en aan de riem trekt.
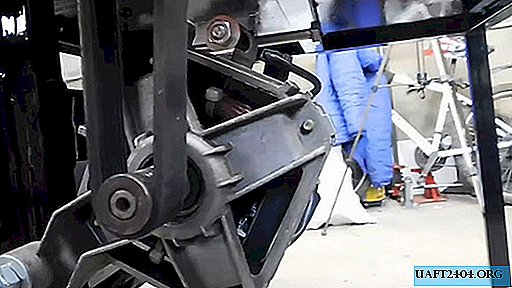

De elektricien bestaat uit een netsnoer, een schakelaar en een spanningsregelaar van de molen. Het verbindingssysteem is vrij standaard.


Bij het opstarten elimineert de aanwezigheid van een regelaar schokken en zorgt voor een soepele reeks omwentelingen door het vliegwiel. Dit is erg belangrijk, omdat de riem niet in de groeven glijdt, wat betekent dat deze langer meegaat.
Dankzij de spanningsregelaar kunt u ook het vermogen wijzigen, wat zonder belasting onmiddellijk tot een toename van de snelheid leidt.
We plaatsen een beschermkap op het vliegwiel om onszelf en mensen in de buurt te beschermen tegen verwondingen als het vliegwiel plotseling van de as vliegt of barst.

Test van een houtsplijter in het bedrijfsleven
Probeer eerst een klein stukje van het bord te splitsen. Met haar, onze zelfgemaakte copes moeiteloos. Hetzelfde gebeurt met droge houtblokken die onder een baldakijn zijn opgeslagen: volledig zonder stress breekt de splitter een vrij massieve hennep af.

Als de "wortel" plotseling vast komt te zitten in een houtblok, dan de stroom uitschakelen, met behulp van een sleutel, de as achter de rug draaien, zonder problemen lossen we het werkgereedschap uit het hout waarin het vastzit.

Zelfs deze kleine praktijk heeft aangetoond dat de wortelsteun op de as moet worden verzonken om het hakken van hout niet te belemmeren en de tafel op een volledig horizontaal oppervlak moet staan. Dit zal zelfs kleine trillingen tijdens de werking van de splitter teniet doen.
Het is ook onmogelijk om aan dit apparaat te werken met handschoenen en wanten, en de mouwen van kleding moeten niet te lang zijn en zonder veters, riemen en andere ophangelementen, zodat ze niet aan de "wortel" draaien en de handen geen pijn doen.

Share
Pin
Tweet
Send
Share
Send